BLOG
AN INTERVIEW WITH ENVIRONMENTAL MANAGER GUY DEVIESE
- #EHS
- #environmental manager
- #interview
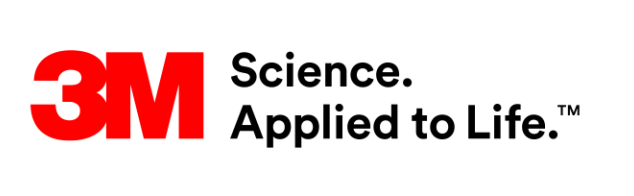
Red-on-line is pleased to introduce one of our clients, Guy Deviese, Environmental Manager at 3M France, who has agreed to…
Red-on-line is pleased to introduce one of our clients, Guy Deviese, Environmental Manager at 3M France, who has agreed to share his experience of working with Red-on-line.
ROL: Maybe to start, you could give us some background on your work with 3M and discuss some of the issues that you faced that led you to work with Red-on-line?
GD: The trigger point for me was when I took the position of Environmental Director with 3M back in 2007. I first started with 3M in 1984 and have worked in various departments in the company. After several years in the internal engineering department, specifically focused on developing the Post-it in France, I took on new responsibilities as the technical director of the Beauchamp site, where the Post-it is manufactured in France. After gaining experience at the plant-level, I transitioned to the director of production operations for Post-it throughout Europe, a cross-functional role at the European headquarters in Cergy, France.
When I accepted the job as Environmental Director, my background was primarily on the operations management side and I did not have a great deal of training in the field of EHS. I realized quite quickly that EHS regulatory compliance is a complex world that can be daunting and difficult to comprehend.

My first challenge was to understand for myself the regulatory requirements for our facilities, particularly on the environmental side, and then figure out a way to transmit this information to our sites. I found out quickly that we had some deficiencies in this area.
Our existing systems relied heavily on rudimentary tools, mainly Excel documents listing regulations, which were difficult to maintain, sync, and keep up to date. My initial reaction was that I must not be alone in this, there must be other companies who face this type of problem, and that there must be someone offering services to support EHS compliance and help companies understand and comply with EHS regulatory requirements.
I began researching available solutions on my own and found the Red-on-line HSE-Compliance solution. Many companies were offering the full outsourcing of services for EHS auditing, but we wanted to maintain some minimum controls of the software and content by our internal EHS team. In comparing bids and solutions, we found the Red-on-line solution to be the most comprehensive.
Once I settled on Red-on-line, I then had to sell the idea to my group in France. Regulatory compliance is a fundamental value to the group, so management immediately came on board for the project.
ROL: What was the implementation process like for you?
GD: It took two years between identifying the need and launching Red-on-line. As many EHS managers know, implementing such a system does not happen overnight. The decision process has several steps. It is first an awakening, a discovery of what was needed, followed by a more detailed assessment, then building a project and business case around the tool in order to deploy the management system internally. Finally, once this was established, we launched a pilot followed by the successful implementation of Red-on-line to all 3M sites across France.
ROL: What were some of the issues you faced during the implementation process? We at Red-on-line understand that when clients begin working with Red-on-line, it is more than just choosing a tool, often you are impacting the processes and working methods at a company.
GD: Absolutely, it is very important to have a project approach. We have an engineering culture at 3M and follow the 6 Sigma methodology. Ahead of launching a project, it is important to identify the need internally and what will be addressed or solved by the project. Moving through a project on a step-by-step approach allows for you to first identify the problem or need, then identify a solution, which allows for a smoother and more effective implementation.

To Sum up:
- The first issue to consider is how to address the fundamental issue of EHS compliance.
- The EHS field is growing exponentially in quantity and complexity. This complexity, clearly noticeable in the regulatory landscape when I first started in the EHS field, is still developing. Despite the simplification and harmonization of speech that we hear, we haven’t perceived any noticeable change or simplification.
- We must therefore remain rational: how can we address the subject in relation to other components of our business, such as competitiveness and the pursuit of minimizing the need for resources, internal, or external, to address the issue? This is how we started.
- Then the question is how do we organize? You must be careful not to believe in miracles because implementation is hard work, it is important to devote the time, energy, resources, and skills to implementing such an important project.
ROL: What systems can be put in place to ensure a smooth roll out of an EHS compliance system?
GD: It is important to identify the proper approach for implementing the project. For us, a tool for managing EHS compliance is essential, because without it, it is impossible to imagine a way to manage regulatory compliance. It is also important not to approach implementation from purely a tool angle, it is necessary to consider all components beginning with the needs and defining a structure for the operational use of the service in every-day life.
At 3M France, we started with a pilot at two sites, followed by implementation across France. The key point is to understand that EHS compliance is a complicated matter that requires time and work, so it is important not to set unrealistic expectations. Be careful with the message that is passed to end-users, we cannot offer some miraculous vision of a solution as it could ultimately lead to failure. We had to highlight that there was a need, which was compliance with EHS regulations, that it is complex, and that there is no alternative but to move forward and do better than how we were doing in the past. The Red-on-line tool helped us in this process and helped us reduce the resources needed to comply with EHS regulations. It also helped us understand some of the more sensitive areas of EHS regulations.
ROL: Today, how is the EHS team at 3M France organized?
GD: We have an EHS manager at each site, and in certain instances there is a separation between Environment and Health & Safety. The manager is the driver of the system and is responsible for inputting data and keeping up with ongoing tasks. To maximize use of the tool requires 3 or 4 site personnel supporting him. We have found that this core is important to the successful deployment of the project. It is important to have fewer people truly engaged in using and implementing the tool rather than having everyone using it, but not entirely certain on its functionality. Conversely, relying on a single person can be dangerous because things can be missed or that person may leave the organization.
We have also found that the HSE-Compliance software continues to improve over time; however, it is important not to dream as the domain is hosting complex information that doesn’t inspire passion (EHS regulations). As such, we are cognizant to deploy responsibly and provide sites with the support they need at the corporate level, while recognizing that it is the site manager who is ultimately the driver who determines success.
ROL: How many 3M sites currently use Red-on-line’s HSE-Compliance Software?
GD: Today we have 16 sites in France on the Red-on-line system. All sites in France are covered except for a recent acquisition. The rise and implementation has been gradual over several years based on the history of EHS problems at each site.
The world headquarters also conducted an analytical review at the international level. The American legal system is more rigid than ours in France, and often regulatory authority is delegated to the states. Because of the size and global image of 3M, the consequences of a regulatory non-compliance are severe, making it imperative to prevent and minimize risk. 3M subsidiaries are also organized in very diverse ways across countries. In fact, our way of managing EHS compliance in France has been cited as an example for global operations as the Red-on-line tool is considered one of the best in the market.
ROL: What is the user feedback to Red-on-line’s services?
GD: The tool provides a good understanding of regulatory requirements and support. One key element is the support of the Red-on-line team. The support available from the Red-on-line team provides additional information about the legal specifications and is widely used by the workers on-site. The EHS managers are generally not legal experts, so it is important to provide regulatory support and help them clearly understand the scope of what they must do. This requires accurate interpretation and a good understanding of applicable regulations.
Coming back to the point of outsourcing as there is always the danger of outsourcing too much and losing ownership or accountability. If you delegate too far, you lose accountability for regulatory compliance. You must respect the regulations and have a collective appreciation for compliance. The regulations are in place for a genuine reason. The most important point for me is that everyone is accountable. The risk of outsourcing is that you lose this feeling of accountability. With Red-on-line as a partner, we retain that accountability and have the support to succeed.
For more detailed information, refer directly to the guidance.
Our EHS experts are at your disposal and will be happy to answer your questions.
We invite you to subscribe to our newsletter.